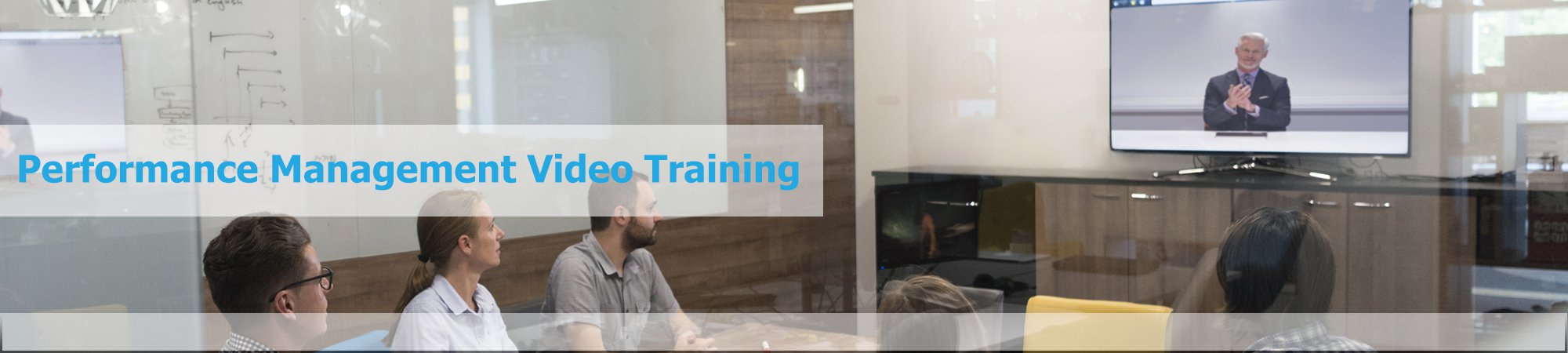
Germ Busters: Ongoing Strategies for Clean & Healthy Facilities
This 58-minute ISSA webinar discusses the strategies for "protecting facility inhabitants from infectious diseases."
View Notes
Video Notes: Germ Busters: Ongoing Strategies for Clean & Healthy Facilities
List of Panelists:
- Kristen Sanchez, Vice President of EHS at SBM Management Services
- Evan Sirlin, Associate Vice President, Core America
- Kimberly Thomas, Senior Director of Services – Facility Management Division, University of Georgia (Retired)
"What have you done to enhance cleaning and ensure infection prevention is part of your organization's plan?" (5:36)
- Written plans / refresher training (for ease of access, whether internally or with external stakeholders) based on industry standards and state regulations
- Implementation of "color-coded program" / training that can be accessed via mobile devices (and in a language of the employee's choice)
- Teaching the difference between cleaning, sanitizing, and disinfecting; implementation of "auditing tools" / quality assurance platforms and methods for detecting invisible sources of contamination (such as ATP testing)
"How do you know it is clean?" (11:22)
- Physical inspection of surfaces and ATP testing; also, audit the cleaning chemicals and their dwell times
- Qualitative scores, preferably an objective measurement tool
- Walkthroughs with customers (to demonstrate what "clean" should be)
Cleaning vs. Disinfecting vs. Sanitizing (13:42)
- Cleaning is "removal of visible dirt" and should be the first step; sanitizing removes some bacteria, and disinfecting also destroys viruses. Exposure of air and surfaces to UV light would be an example of a disinfecting method.
- Merely using a disinfectant does not necessarily qualify as "disinfecting" unless (a) the dwell time requirements are met, and (b) the surface is cleaned first
How to identify "infectious reservoirs"? (17:28)
- While people often think of restrooms as a problem area, one should instead focus on the areas in which people spent the most time
- High-touch points and "dark and wet spaces" are also areas of concern
- Also consider "personal work spaces" that are typically skipped by janitorial service providers
Cost of "Regular cleaning" vs. "Infection prevention" (22:47)
- Realistically, it is "both / and": Infection prevention should be a goal of regular cleaning, as not keeping your facility healthy for its occupants would ultimately have negative financial consequences
- The choice of disinfectants and cleaning equipment can be a potential source of savings if productivity can be increased
- "Green cleaning" as an approach for cleaning for health
Considerations for selecting and maintaining cleaning equipment (26:57)
- Cleaning equipment can actually be a source of cross-contamination if they are not being properly cleaned / maintained themselves
- New technology can be helpful, but do they actually increase productivity further relative to the status quo? ("Are they really advances?")
- Sustainability considerations apply to both chemicals and equipment
"How do you empower staff to do more with less and still maintain cleaning quality?" (30:55)
- Cleaners need to be "trained on the why" and hear that "they're part of a team that saves lives"
- Ensure proper workload for cleaning staff, and listen to feedback from them
- Pay them a competitive wage, and consider removing certain tasks from the custodians' responsibility if possible
- Invest in more efficient equipment ("work smarter")
How to train staff to use cleaning products properly? (37:23)
- Limiting to ready-to-use products may make sense, as this reduces preparation time and removes one source of human error (such as improper dilution)
- Consider adopting Green Seal-certified products (which are safer for people) and chemicals with shorter dwell time; SDS sheets need to be properly maintained
- There should be an audit process; in case of a performance drop, provide remedial training that's non-punitive
Q&A Session (44:22)
- Chemical vs. "mechanical" disinfection: Both are important, in the sense that a surface needs to be properly wiped down before applying a disinfectant. Also consider the type of surface and "what do you think is on there"
- How to persuade the client to "allocate the right resources for proper cleaning and disinfection"? The service provider may be forced to absorb the extra cost in some cases, but that is exactly why the client should be involved in the auditing process (show them the results, not just tell them). Also be clear on the expectations in the scope of work– extra services can and should be charged separately, and educating the client on the "why" is important. Finally, the cleaning staff "are actually the best ambassadors" if they understand the importance of what they are doing.
- Using touchless cleaning systems / ionization equipment, etc.for disinfection: They can be useful, but surfaces still need to be cleaned first (for example, mist-generating disinfection systems are not a substitute for "removing dirt and grime from the surface"). Also, "do your research"– there should ideally be third-party confirmation of the efficacy claimed by the manufacturer, and you need to be "using the right chemical" in the first place.
- How should cleaning equipment themselves be properly cleaned / maintained? They should be cleaned "after each use," and there should be both a pre-inspection and a post-inspection; the chemicals used in the cleaning process can be used on the cleaning equipment as well (if appropriate). Also, read the instructions!