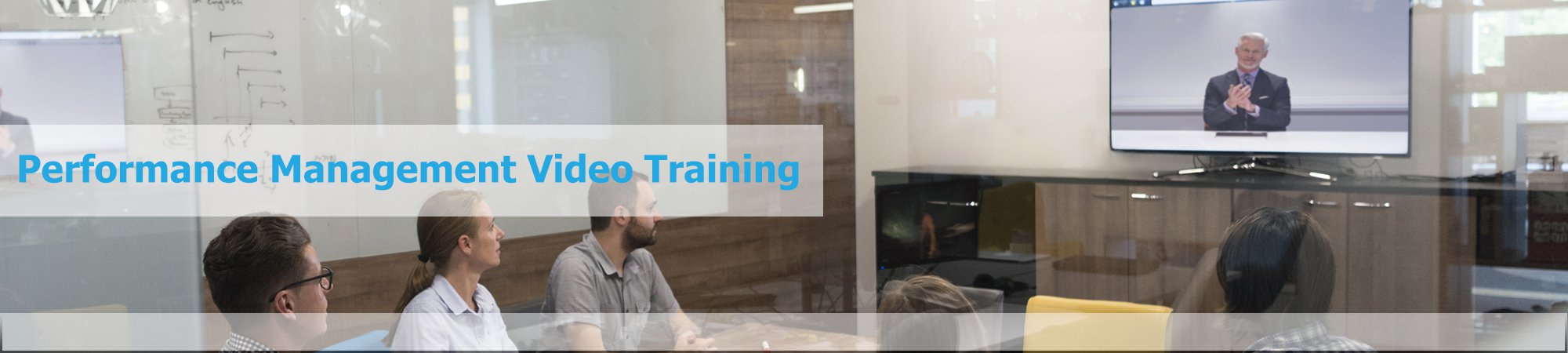
Defining Quality and Recording Common Defects
In this 30-minute video, Ron McCuen goes into the details of how common defects should be recorded as part of the inspection process.
View Notes
Video Notes: Defining Quality and Recording Common Defects
What to inspect / General considerations for recording defects
- In general, every type of item listed for a room should be inspected if possible. However, only a subset of the same type of item needs to be checked– one does not need to examine every single chair in a classroom or auditorium, for example. Broad groupings can also be used for ease of aggregate analysis (e.g. “Wall Box” as opposed to separating out the contents).
- If an item has no attributes indicating that it is not clean, it should be marked as “satisfactory”; otherwise, a specific defect should be recorded, and the defect must be provable in some way. Note that defects that occur on multiple items should be recorded separately for each type of item.
- If a type of item has multiple defects, use the most comprehensive description that is applicable to the situation. For example, dispensers within restrooms should first be checked to see whether they are properly stocked; “unstocked dispenser” takes higher priority over cleanliness issues, as it is assumed that the dispenser would also be cleaned as part of the restocking process. Likewise, an item that has dust, cobwebs, AND residue on it should be marked as ”residue,” as addressing the residue issue should also resolve the other two defects.
Guidelines for specific types of items
- Carpets and other floor surfaces should be treated separately from their corners and edges. If spots are found on carpets, check the condition of the spots; in most cases, those spots should be counted as routine cleaning defects unless they are wet (i.e. too recent to be the cleaning system’s fault), or are actually stains that could be removed despite being cleaned repeatedly (which would be marked as maintenance defects instead). Go to the 14-minute mark for descriptions of common defects for carpet corners and edges.
- Likewise, streaks on floors should be investigated further to determine whether they are a mopping issue or a project work issue (go to 15:29 for more details). For a list of common defects for floor corners and edges, go to 16:50.
Other considerations
- Certain defects are considered “maintenance” defects; they do NOT count against the overall cleanliness score because they are technically not caused by deficiencies in the regular cleaning process. (Common examples include non-functional equipment, leaking pipes, and rust.) One may also mark an item as “waived” to indicate “there is a cleaning-related defect, but we will not count it due to extenuating circumstances” (such as construction or other limitations to the extent that the item can be cleaned).
- The client may also further fine-tune the setup for a site via the usage of item weights, to indicate that certain items are more “important” than others. (Typically, floor surfaces would be given extra weight by treating them as the equivalent of 2+ items.)
- While customer satisfaction is subjective, it provides another measure of how cleanliness performance is perceived by a building’s occupants. Ideally, there should be at least 1 consumer rating per 4 rooms inspected; if possible, ask for more details on what people think the problem is (and when the problem occurs).
Tags:
training